January 03, 2023
On December 7, during the Rendez-vous ED (Events for ED), the HEC Montréal Executive School organized a webinar on the theme of Supply Chains: Anticipating the Unpredictable. Luc Bourdeau, Vice-President, Supply Chain, at the SAQ, explained how the government corporation managed the complex issues and unforeseen events caused by the pandemic.
Serial worries
In March 2020, as the COVID-19 pandemic hit Quebec hard, the government put the economy on hold and instituted a strict lockdown. Despite this situation, all SAQ branches remained open to serve customers.
The state-owned company, accustomed to handling over 25 million cases annually, is nevertheless having to deal with sudden product shortages. Some wine-exporting countries, such as South Africa, are banning alcohol exports. Others, such as New Zealand, are cut off from the world: containers are no longer reaching them. The SAQ's warehouses in Montreal and Quebec City are emptying rapidly.
Additionally, at the start of the pandemic, shipping companies began canceling container orders and laying up ships, reducing shipping capacity. Labor shortages at several ports also caused ships to be tied up at their destination, containers to remain on the docks, and the cost of shipping goods to skyrocket.
As if that weren't enough, elsewhere, such as in France, frost episodes are affecting harvests. Many supply chain employees must self-isolate at home to comply with government guidelines and prevent the spread of COVID-19. A shortage of dry goods is also hitting Europe, particularly for bottles (impacted by the war in Ukraine), corks, and even wooden pallets. And here in Canada, Canada Post is stopping home parcel deliveries due to the discontinuation of proof of age verification for home deliveries.
How, in the midst of all these complications, can the SAQ ensure the fluidity of its supplies?
Transform, and fast!
"Normal models were no longer working; we had to turn around overnight," says Luc Bourdeau. "We went from a just-in-time predictive model to a just-in-case model!"
The situation is further complicated by two factors: online sales are exploding, while those in the restaurant sector are grinding to a halt. These sales will pick up again during the partial summer reopening, only to slow down again during the second wave in the fall; they now exceed pre-pandemic volumes.
"We had to increase SAQ.com's capacity to maintain order processing times, which reduced our product offering. We also had to protect inventory for the reopening of restaurants, while the wine selection had shrunk and spirits were piling up on shelves," he continues.
The SAQ also had to deal with irregular arrivals of containers at the Port of Montreal.
"Normally, we have space at our Montreal site to store 150 containers awaiting receipt," he says. "One morning, a boat showed up with more than 200 containers on its own!"
The state-owned company was therefore forced to store containers at external sites.
Adjust promotions
Planned promotions had to be constantly adjusted based on last-minute inventory changes. Product alternatives had to be offered based on category, quality, region, and retail price.
“Throughout the pandemic, we had to manage uncertainty: would consumers visit branches, shop online? Would summer tourism increase demand in the hospitality and restaurant sectors? The prevailing ambiguity constantly forced us to manage several variables at once.”
Maintain the customer experience
To maintain the customer experience, the Crown corporation was forced to adjust its entire supply chain, starting with enhancing the role of the Quebec City warehouse. SAQ.com's capacity was increased. And Purolator took over from Canada Post for home deliveries.
In branches, advisors played a key role in directing customers to the right products. And on the producer front, it was necessary to secure supplies:
"We have established a weekly monitoring charter by country and producer to track the situation," says Luc Bourdeau. "For example, if we can no longer receive products from a French producer, we will fall back on products from Portugal or Argentina."
Back to normal
The SAQ is currently managing a gradual return to normal, operating on a just-in-time basis. Despite ongoing container problems, high shipping costs, inflation, a labor crisis, and energy problems in some parts of the world due to the war in Ukraine, the SAQ has managed to maintain high inventories in its warehouses to meet its customers' needs.
"We have learned to move forward in unpredictable circumstances, using project management principles and internal multidisciplinary teams collaborating with external resources," explains Luc Bourdeau.
The SAQ is also working on its long-term transformation, including automation and expansion of its Montreal distribution center, to ultimately enhance online sales by offering up to 20,000 products:
“In a multi-channel environment where fast delivery and full availability of products offered to customers are the norm, we want to meet our customers’ expectations,” concludes Luc Bourdeau.
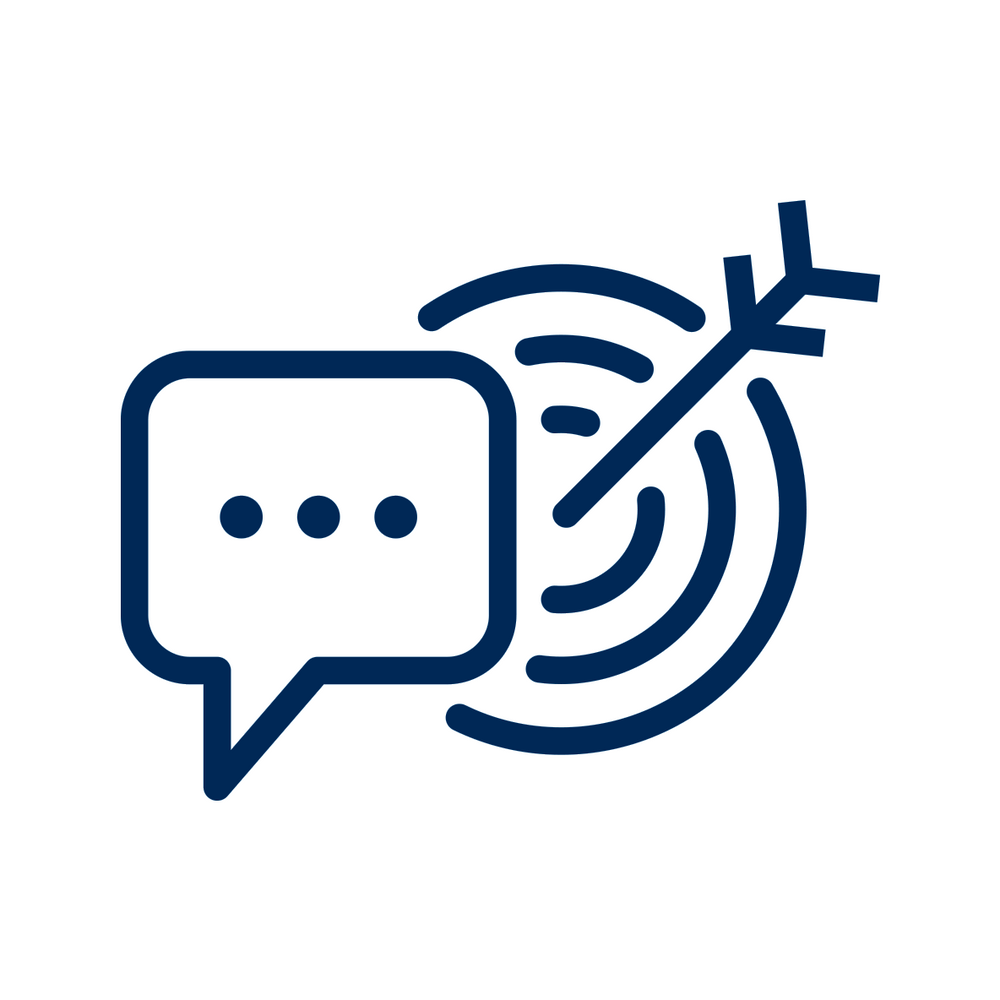
Discover our Certification in Retail Management offered in collaboration with the SAQ
Explore all courses
Learn more about our upcoming events